Behind the Scenes at the Tricker’s Shoe Factory
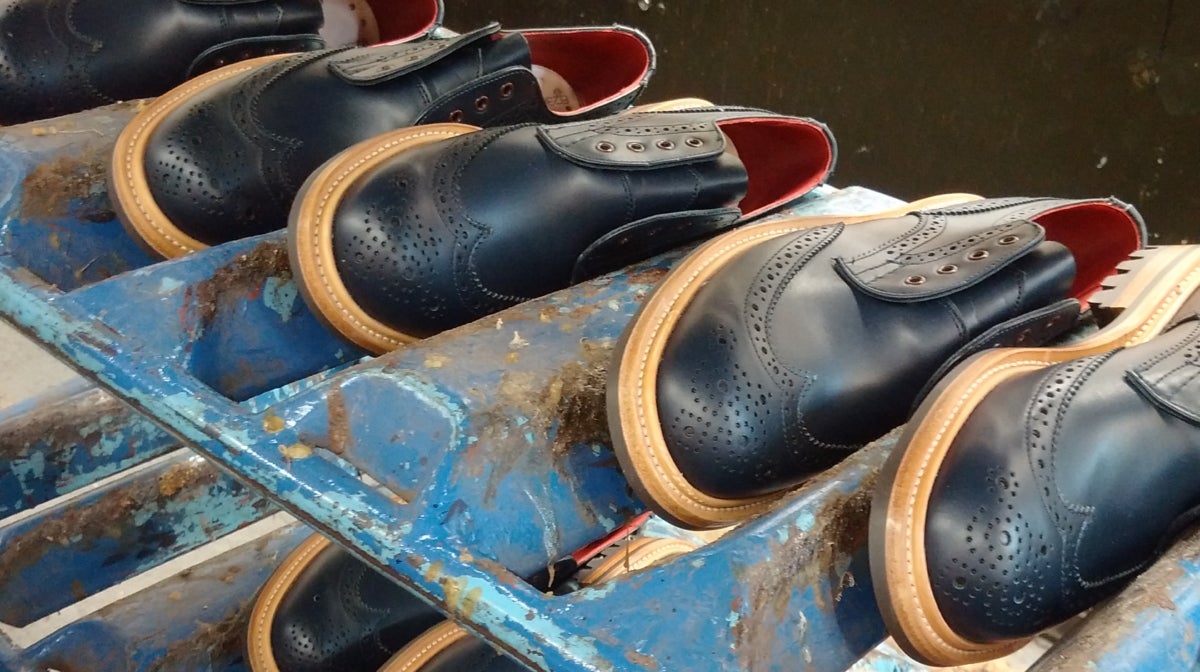
A brand that requires no introduction among footwear aficionados, Tricker’s has been handcrafting some of Britain’s finest shoes and boots from its homestead in Northampton for almost 200 years. Since the very beginning, Tricker’s has retained a core focus on premium quality materials and meticulous craftsmanship, building a reputation as one of the country’s most prestigious shoemakers. Counting politicians, soldiers and leading figures in the arts among its wide range of customers, the company has also been honoured with the Royal Warrant from His Royal Highness The Prince of Wales, and has been a supplier to his household now for over 25 years.
Using a time-honoured process that remains virtually unchanged over almost two centuries, the team of cobblers at Tricker’s gave us an insight into the history, heritage and traditions of British shoemaking. We joined the brand for a tour of the iconic Northampton factory and an insight into the art of shoemaking.
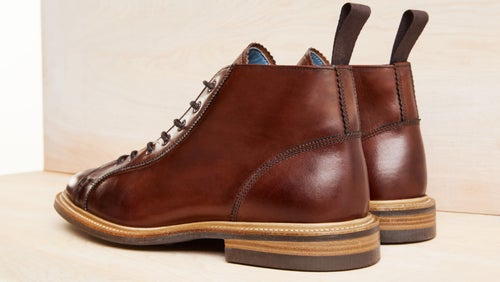
A Closer Look at the Tricker’s X Knutsford Collaboration
A brand that requires little introduction, Tricker's recently teamed up with Cheshire-based brand Knutsford to produce an exclusive collection celebrating traditional British craftsmanship. We take a closer look at the collaboration.
First Stop: The Clicking Room
Clicking marks the first stage in the production of welted leather footwear. Here the high-quality calf leathers and suede leathers, already sorted into batches, are carefully cut to take on the shape of the upper. The role of the clicker is to analyse any defects in the animal skin and to then go around those defects to create clean and tidy uppers.
Step Two: The Closing Room
This is where the form of the upper truly begins to take shape. Filled with skilled workers representing centuries of shoemaking experience plus many complex machines, the closing room is where many famous processes such as skiving, punching, gimping and fitting take place. Here all the different elements that make up the upper—from the serrated detailing or perforations on a brogue to the sewn details on a boot—take place and come together to begin to create the unique shape and character of the shoe.
Step Three: The Lasting and Making Room
Once the closed upper comes through to the lasting and making room, it is first put into a wooden last. The full unit of the shoe then comes into being as the upper of the shoe is built on by stitching a welt in, adding a sole unit, and then putting a heel onto the sole.
Step Four: The Finishing Room
With the shoe now fully formed, it is now passed on to the Finishing Department to bring out the natural colour of the leather and refine the quality of the shoe. Each pair is hand finished by one of Tricker’s expert shoemakers, who trim the soles and heels and buff the edges until they are smooth. It can take years of experience and a meticulous eye to master this traditional freehand skill. The brand’s craftsmen and women then stain, polish and wax the leather uppers to create a waterproof finish, before ‘bunking’ the soles by adding decorative patterns with tools heated over a naked flame.
Step Five: The Shoe Room
With the shoe now virtually complete, it comes to the final part in the factory process: the Shoe Room. Here a sock liner is fitted to the shoes or boots for comfort. The finished pair is then cleaned, and the uppers are dressed to create a patina using a unique blend of creams and polishes. After hanging overnight one last time to moisturise, the shoes or boots are polished and burnished by hand to give them their final distinctive lustre. Then they must pass a final inspection before they are laced, wrapped in cotton cloth and packed into their box together with their Tricker’s shoe bags. After 260 different processes, all carried out by hand, another pair of Tricker’s handmade shoes or boots are finally ready to be delivered to you.
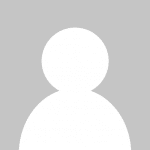